In May 2022, the joint project of the Abinsk Electrometallurgical Plant and the Russian company Datana (part of the LANIT group) was completed. The goal of the project is to reduce the consumption of deoxidizers, ferroalloys and slag-forming materials by reducing the ingress of furnace slag into the steel ladle during the tapping of the melt from the EAF.
The control of the steel production process from EAF was previously carried out on the basis of a visual assessment of the steelmaker. The steelmaker watched the flow of steel through goggles and focused on its color, noise, sparks and his experience. The conditions of the melt tapping process are accompanied by a high degree of smoke, which often does not allow even an experienced specialist to accurately determine the moment of slag penetration. This leads to the fact that, together with the metal from the EAF, peroxidized furnace slag enters the steel-pouring ladle.
To reduce the ingress of furnace slag into the ladle, Datana has implemented a comprehensive solution of its own design, Datana Sense, in the EAF. Slag detection at the outlet. The solution monitors the release of steel, visually highlighting the slag in the stream, and when the permissible level is exceeded, it issues a light and sound signal. The release is controlled by a far infrared camera that allows you to "see" through the smoke, and an artificial intelligence module that accurately detects the presence of furnace slag in the stream.
The solution is designed for industrial production. The infrared camera is protected by a heat-resistant housing, and uses an air barrier in the front of the housing to protect the window from contamination. The built-in self-diagnosis system continuously monitors the performance of all elements. On the control panel there is a monitor that visualizes the melt tapping process and a light and sound column.
Video recordings of all issues are stored in the technological archive and are available for analysis and technology adjustment.
According to the expert assessment of AESW specialists, as a result of the introduction of Datana Sense, the potential savings of deoxidizers, ferroalloys and slag-forming materials can be 10%, and the reduction in electricity consumption up to 5%.
In addition, within the framework of this project, the joint operation of the Datana Sense digital solution with the solution for issuing recommendations for the addition of ferroalloys during the finishing of the melt at the ladle furnace was set up. The solutions were combined into a single value chain.
Vladimir Zakharov, CEO of Datana: “In this project, we applied our approach to end-to-end digitalization, for the first time combining our digital advisor with an advisor from another company into one value supply chain. This solution has a synergistic effect and will allow us to achieve significant savings on expensive alloying materials.”
Anatoly Maslov, IT director of the Novostal-M holding: “Novostal-M has a great, not yet fully realized potential in improving the efficiency of its enterprises. We are going to fully open it through the use of modern digital technologies that can significantly reduce costs and increase productivity. It's nice that Russian companies, including Datana, are helping us with this."
AESW implemented digital technologies for detecting slag in a steel stream jointly with Datana
Press Releases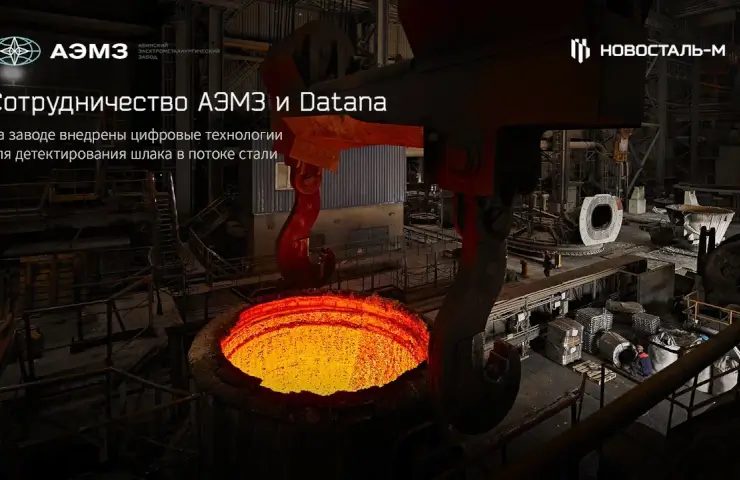
Сomments
Комментарии (0)
On this topic