ESAB, one of the leaders in the production of welding materials and equipment for welding and cutting, has reduced the repair time of ship shafts by 70 %. The shipyard, which operates with propeller shafts weighing 50 tons and 25 meters long, turned to the company, because the existing equipment at the enterprise did not provide proper stability of the process.
The steels used in shipbuilding are particularly sensitive to heat and have a high price – they can contain manganese, chromium, nickel, molybdenum, niobium and vanadium. Excessive heat input can lead to deformation of the shaft and deterioration of its mechanical properties, which will significantly reduce the service life. For these reasons, particularly strict requirements are imposed on the quality of welding.
ESAB has installed a shaft surfacing system based on the LAF 1001 welding current source. Surfacing is carried out with a heavy-duty welding head A6, which is mounted on a carriage with the ability to move along the surfaced surface for a length of 2.2 m. The device is equipped with a flux feed and recirculation system. Surfacing of shafts with a diameter of 100 to 1200 mm is made with high-alloy wire with a diameter of 3 mm. The shaft is rotated by a set of roller supports with a total load capacity of 60 tons. Another set of supports can rotate shafts weighing up to 135 tons.
Due to the difficulties associated with positioning the 50-ton shaft, moving it to the roller stand for automatic surfacing requires "astronomical" costs. An alternative is to repair using a manual or semi-automatic process, which leads to surfacing variability - deviations from the required geometry, which is practically eliminated when using ESAB technology.
Also, the ESAB system is easy to operate – all the parameters of surfacing and moving are programmed in the controller, so the operator only needs to position the welding head and start the process.
In addition to repairing the propeller shafts, the shipyard regularly repairs sheets up to 80 mm thick. Usually, when welding thick-walled metal, the process requires sampling the root of the seam to ensure 100% penetration. To increase productivity, the shipyard purchased four ESAB A2N Multitrac welding tractors with two replaceable heads each: a single-wire submerged welding head and a specially modified Arcair ® N7500i head for coal gouging.
The A2N Multitrac tractor allows the operator to weld one side of the plate using a submerged arc welding process, turn the sheet over, change the head to a suitable one for gouging, and perform gouging on the reverse side. After another quick change of the welding head, the operator completes the welding of the joint.
"No operator, working manually, can compare with an automatic system in terms of the repeatability of the thickness of the surfacing or the control of the level of heat input. For this reason, a proven process has been adapted for the restoration of ship shafts, which has long proven itself in steel mills, " says Dmitry Kuraksa, Managing Director of ESAB in Russia and the CIS.
Seven feet under the keel: ESAB increases the speed of repair of ship's shafts by 70 %
Press Releases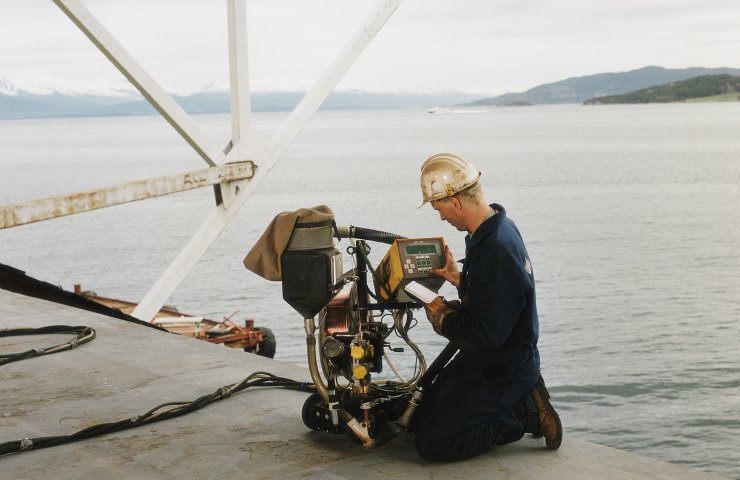
Сomments
Комментарии (0)
On this topic