Moscow, February 10, 2021-A European manufacturer of car lifts has increased the efficiency of the welding process by 600 % after installing a rotary welding machine (FSW) from ESAB, one of the leaders in the production of equipment and consumables for welding and cutting.
In 2011, the company set a goal to reach a new level in the production of lifts with a large working radius and lifting capacity. As a result of the project, it was possible to increase the welding speed to 6 m/min, while the classic MIG/MAG process, which was used before, provided a maximum speed of up to 1.5 m/min.
Mixing friction welding is widely used for joining aluminum alloys, as well as copper-based alloys. FSW is widely used in the aerospace, shipbuilding, and automotive industries, and is gaining popularity in bridge construction. Today, ESAB is working on the possibility of applying the technology for welding steel products in industrial conditions.
Unlike traditional methods, the FSW process does not require welding materials and shielding gases. It is highly energy-efficient and allows welding with almost complete absence of deformations. At the same time, one tool for the FSW installation makes it possible to produce up to 2000 m of weld.
ESAB's FSW installation allowed for the production of lighter and stronger lifts, allowing the customer company to expand its product range with longer booms and increased lifting capacity.
The second FSW machine installed in 2019, as well as the modernization of the control system of the previously delivered machine, reduced labor costs, since now the company's operator works simultaneously on two installations.
In addition, the use of rotary friction welding technology with mixing has improved the quality and stability of the process of manufacturing metal structures and significantly reduced the amount of repair of welds.
"Mixing friction welding is ideal for working with aluminum-based alloys, but it has its own characteristics that need to be taken into account when designing equipment. We approach each project individually: we take into account the dimensions of the products, take into account the thickness, the type of alloy, the location of the seams and other important parameters. This depends on the characteristics of the installation, and the tool for it. As a result, the customer receives a solution that is ideally suited to their needs and gives a tangible result – a significant increase in productivity and improvement in the quality of manufactured products, " comments Maxim Ponomarev, head of the Automatic equipment Department at ESAB.
At the top of efficiency: ESAB technology has increased the productivity of welding production by 600%
Press Releases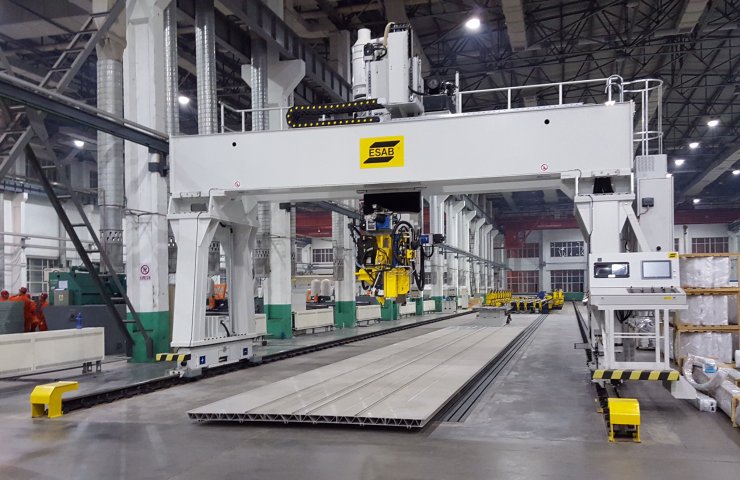
Фото: ESAB
Сomments
Комментарии (0)
On this topic