In the scientific and technical steel laboratory of the Stary Oskol Technological Institute named after A.A. Ugarov, a branch of NUST MISIS, located on the territory of the Oskol Electrometallurgical Plant (OEMK, part of the Metalloinvest company), metallurgists, together with scientists from the institute, carried out a set of works to develop a new steel grade for OEMK. We are talking about economically alloyed chromium-manganese steel. "The new steel grade was developed specifically for the Slovak company HKS, a leading manufacturer of forgings and stampings in Europe used in the automotive and mechanical engineering industries," said Ivan Malikov, Head of New Products at OEMK. “Interaction with the institute allowed us to confirm the whole range of technical requirements imposed by the NKS company.” As explained by the head of the laboratory, head of the Department of Metallurgy and Metallurgy named after S.P. Waste STI NUST MISIS Aleksey Kozhukhov, 37 melts were carried out to select the chemical composition of steel to meet the customer's requirements for mechanical properties, hardenability and operational characteristics of the finished product. MISIS employees developed a mathematical model capable of predicting the dependence of metal hardenability and mechanical properties on chemical composition of steel. This allows metallurgists to develop the technological process in such a way as to guarantee the high quality of the final product. "Today, Metalloinvest faces a serious task - the improvement and development of innovative, high-tech steel grades, unique alloys by customer orders," said First Deputy General Director - Director for the production of MC "Metalloinvest" Andrey Ugarov. “About 300 steel grades are smelted at OEMK every month and work is constantly underway to expand the range of brands, including as part of a comprehensive program to improve customer focus and quality SBQ.” Metalloinvest and NUST MISIS have invested in the creation of a scientific and technical steel laboratory, launched in 2018 year, more than 60 million rubles. The laboratory's vacuum-induction furnace with a maximum load of only 60 kg allows you to quickly carry out experimental melts in small volumes, which are impossible in OEMK industrial 150-ton furnaces. This allows OEMK specialists to carry out more experiments and significantly reduces research costs.
OEMK is mastering the production of new steel grades by customer orders
Press Releases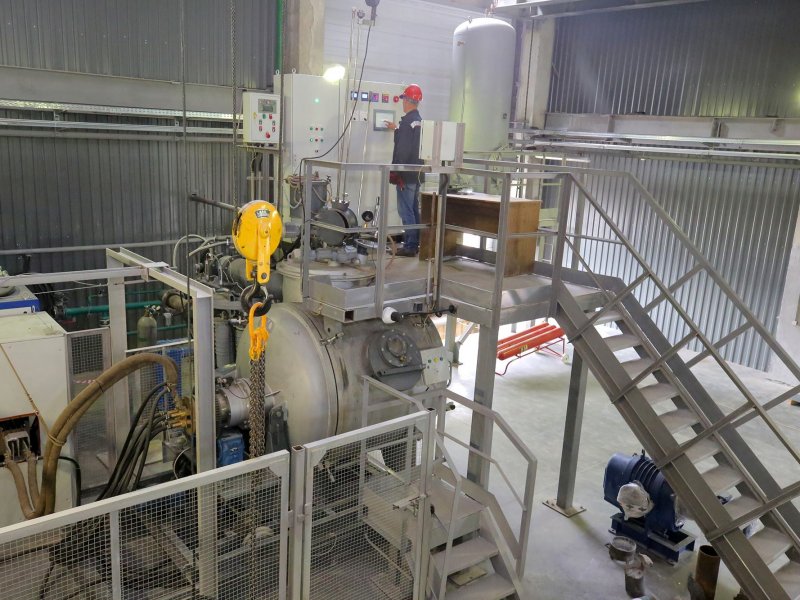
Сomments
Комментарии (0)
On this topic